Did not you find what you were looking for? Ask us! We have archives of 140 TB. We have all modern reuse projects and renovation projects for Soviet standard buildings. Write to us: info@proekt.sx
Boiler project 8000 kW
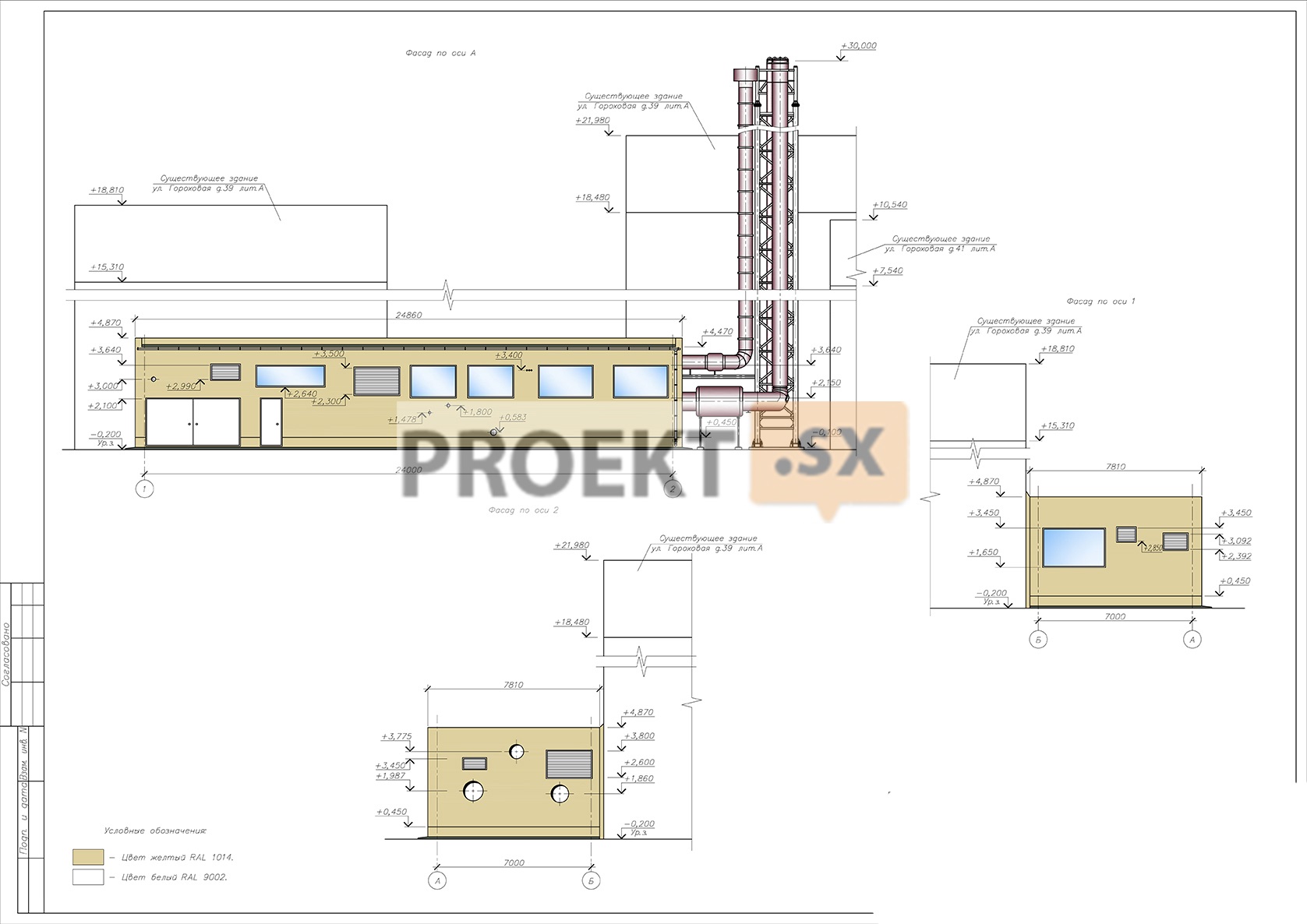
Design, working documentation without estimates and the results of engineering surveys for the construction and reconstruction of thermal power facilities. Construction of a boiler house.
Technical and economic characteristics of the capital construction object
Land area, m2: 301,0
Building area, m2: 215,38
Total building area, m: 168,0
Construction volume of the building, m3: 913,71
Number of floors, floor: 1
Productivity, kW: 8000
Length of engineering networks, including: lm: 2196,99
heating networks, r.m.: 1783,34
water supply networks, lm: 257,45
sewerage networks, lm: 47,7
power supply networks, lm: 23,0
gas supply networks, lm: 26,5
communication networks, r.m.: 59,0
Architectural and construction solutions
Architectural and design solutions are presented in the drawings of the brand 108-829-3/11-AS, 108-829-3/11-KZh and 108-829-3/11-KM. The boiler room belongs to the explosion and fire hazard category "G" in accordance with SNiP II-35-76. The degree of fire resistance of the boiler house is I. The climatic region of construction according to SNIP 23-01-99 * "Construction climatology" - 11b. The normative value of the weight of the snow cover for the III snow region according to SNIP2.01.07-85 "Loads and impacts" is 126 kgf / m2. Standard wind pressure for the II wind region according to SNIP 2.01.07-85 "Loads and impacts" - 30 kgf/m2. The temperature of the coldest five-day period is t=-26°C. For a relative mark of 0,000, the level mark of the clean floor of the boiler house was taken, which corresponds to the absolute mark of +3.67, adopted in the Baltic system.
Technological loads from equipment
The building in plan is a rectangular structure with dimensions in the axes: the length of the building is 24 m; width - 7 m; floor height - 3,9 m; Construction volume V = 873,33 m3; Total area S = 168 m2; Building area S = 194,16 m2. The outer walls are made of bricks (1,5 bricks - 380 mm), thermally insulated from the outside with mineral wool (50 mm), plastered and painted from the outside, painted from the inside. The partition is made of bricks (0,5 bricks - 120 mm), painted on both sides. The masonry of the inner part of the wall is made of face brick KORPu 1NF/200/1,4/50 for jointing, the rest of the masonry is made of ordinary brick KORPu 1NF/200/1,4/50/1. The laying of the basement part of the building is made of solid brick KOLPO 200NF/2,0/50/1, above the basement part - of hollow brick KORPu 200NF/1,4/50/1. The masonry of the partition is made of facing brick KOLPu 200NF/1,4/50/120 for jointing. Covering - insulated roll roofing, on a reinforced concrete slab, 150 mm thick, with an organized external drain. Thermal insulation of the roof - Rockwool "RUF-BATTS" slabs, 211,10 mm thick. The area of the exterior finish of the boiler building is 2 m1.436.420. Windows - made of aluminum profile, analogue of the standard project according to the series 31173 "Windows with aluminum alloy bindings for industrial buildings". Door blocks are supplied in accordance with GOST 2003-31174 "Steel door blocks". Gates are supplied in accordance with GOST 2003-948 "Metal gates". Lintels are supplied in accordance with GOST 84-0,03 "Reinforced concrete lintels for buildings with brick walls". Floors from sparkling materials. The boiler house is provided with easily dumped structures at the rate of 2 m1 per 3 m22 of the volume of the boiler room. Their role is performed by window blocks with a total area of 2 m1. The foundation for the boiler room is a monolithic slab PLm1,5. For the introduction of engineering networks in the foundation structure, two pits are provided. One with dimensions of 4,485 m x 1,41 m x 1,5 m, the second - 1,1 m x 2,12 m x 1,8 m. The foundation for the FTM chimney is piled, designed as a pile bush with bored piles, combined solid monolithic grillage, the height of the grillage is 25 m. The grillage is made of concrete B6 W75 F50. The connection between the piles and the slab is rigid, with the pile head embedded by 22.13330 mm. in accordance with SP 2003-XNUMX.
Thermal mechanical solutions. layout solutions. Description of the thermal diagram of the boiler room.
As the main equipment of the boiler house, two boiler units 02L.02.02GD3.01.07L-5000 with a thermal power of 5000 kW (pos. K1) and 02P.02.02GD3.01.06P-3500 with a thermal power of 3500 kW (pos. K2), manufactured by 3NTROROS. Boiler units are equipped with combined burners GKP-500M (for pos. K1), GKP-400M-I (for pos. K2), manufactured by Oilon, as well as pump groups manufactured by Wilo with a set of shut-off and control valves. All imported materials and equipment are certified for use on the territory of the Russian Federation. For the operation of the heat supply system in the specified modes, the following types of auxiliary equipment were selected (for a detailed description, see Fig. 108-829-3/11-TM): Plate heat exchanger M15-MFM (pos. K17, K18) for a heating system with a capacity of 8,278 MW each, manufactured by Alfa-Laval. Operating mode - 1 working + 1 standby; Plate heat exchanger TL3-BFG (pos. K19, K20) for the DHW system, with a capacity of 0,09 MW each, manufactured by Alfa-Laval. Operating mode - 1 working + 1 standby; Network circulation pumps BL 80/165-22/2 (pos. K7, K8, K9), with a frequency drive, for a heating system, with a flow rate of 152 m3 / h and a pressure of 0,333 MPa each, manufactured by Wilo. Mode of operation - 2 workers + 1 standby; Recirculation pumps MVI 102/PN16-3 (pos. K12, K13), for a DHW system with a flow rate of 0,48 m3 / h and a pressure of 0,174 MPa each, manufactured by Wilo. Operating mode - 1 working + 1 standby; Circulation pumps IL 100/145-11/2 (pos. K4, K5, K6) of the boiler circuit of the heating system, with a flow rate of 190 m3 / h and a pressure of 0,162 MPa each, manufactured by Wilo. Mode of operation - 2 workers + 1 standby; Circulation pumps IPL 25/80-0,12/2 (pos. K10, K11) of the boiler circuit of the DHW system, with a flow rate of 2,75 m3 / h and a pressure of 0,064 MPa each, manufactured by Wilo. Operating mode - 1 working + 1 standby; Make-up pumps MHI 205 3~ (pos. K15, K16) of the boiler circuit of the heating system and hot water supply, as well as the network circuit of the heating system, with a flow rate of 2,07 m3 / h and a pressure of 0,43 MPa each manufactured by Wilo. Operating mode - 1 working + 1 standby; Booster pumps MHI 805 3~ (pos. K14.1, K14.2) on the water supply line, with a flow rate of 9,07 m3 / h and a head of 0,25 MPa each manufactured by Wilo. Operating mode - 1 working + 1 standby; Expansion closed membrane tanks ERE CE 1000 (pos. K24, K25) on boiler units with a capacity of 1000 liters each, manufactured by CIMM. Expansion closed membrane tanks Flexcon CE 1000 (pos. K26, K27) on a heating network, with a capacity of 1000 liters each, manufactured by CIMM. Dosing unit TEKNA TPG 603 (pos. K34, K35) for the treatment of make-up water of the boiler circuit of the heating system and hot water supply, as well as the network circuit of the heating system, manufactured by Seko. The thermal scheme of the boiler house is selected according to an independent scheme through plate heat exchangers (two for the heating system and two for the DHW system), with the temperature of the coolant in the network circuit of the heating system adjusted according to the outside air temperature and maintaining the set temperature in the DHW system. Regulation of the parameters of the heat carrier of the heating system (pos. 45) and DHW systems (pos. 46) is carried out using three-way valves with actuators located directly in the boiler room. For hydraulic decoupling of the boiler circuits of the systems, a hydraulic switchgear designed and manufactured by ENTROROS LLC is used. The circulation of the heat carrier in the boiler room is carried out by boiler and network pumps of the company "Wilo" (Germany). The thermal diagram of the boiler house was developed based on the recommendations of the main equipment manufacturers - Entroros, Oilon, Wilo, dmm, Flamco, Alfa Laval. The supply of cold water for preparing hot water and feeding the boiler room systems is supposed to be from two inputs with the installation of shut-off valves: Water metering units TsIRV02A.00.00.00 are installed on each of the inputs. ll. 52, 53. The tap water entering the boiler room enters the iron removal filter, after which it goes to the chemical dosing unit and then to feed the network and boiler circuit of the heating system. Cold water for the DHW system enters the heat exchangers of the corresponding system without chemical treatment. reagents. To maintain the required volume of water in the boiler circuit of heating and hot water systems, as well as the network circuit of the heating system, caused by the possibility of leaks, the project provides for automatic make-up from the water supply. The performance of water treatment is selected at the rate of 0,75% of the volume of heat networks in accordance with clause 6.16 SNiP 41-02-2003 "Heat networks". Heating networks are initially filled with prepared water. To prevent deposits from the heating network from entering the boiler circuit of the boiler room, sludge traps OISm 150/25 (pos. K32). Compensation for the thermal expansion of the coolant - water in the boiler circuit is carried out in expansion tanks (pos. K24, K25) with a volume of 1000 l each; in the network circuit of the heating system - in expansion tanks (pos. K26, K27) with a volume of 1000 l each; at the feed of the boiler circuit - in expansion tanks (pos. K28) with a volume of 100 liters. The preparation of the heat carrier is carried out in boiler units, which are equipped with an automation, control, regulation and safety system. The temperature control of the heat carrier in the boiler circuit of the heating system, as well as maintaining the set temperature in the DHW system, is provided by three-way control valves with actuators DN 150 mm and K "respectively. To prevent a possible increase in pressure in the boiler circuit, two safety valves are installed on the boiler units.