Не нашли что искали? Спросите у нас! Имеем архивы на 140 ТБ. У нас есть все современные проекты повторного применения и проекты ремонта советских типовых зданий. Пишите нам: info@proekt.sx
Завод по производству пенополиуретановых компонентов сидений для автомобилей
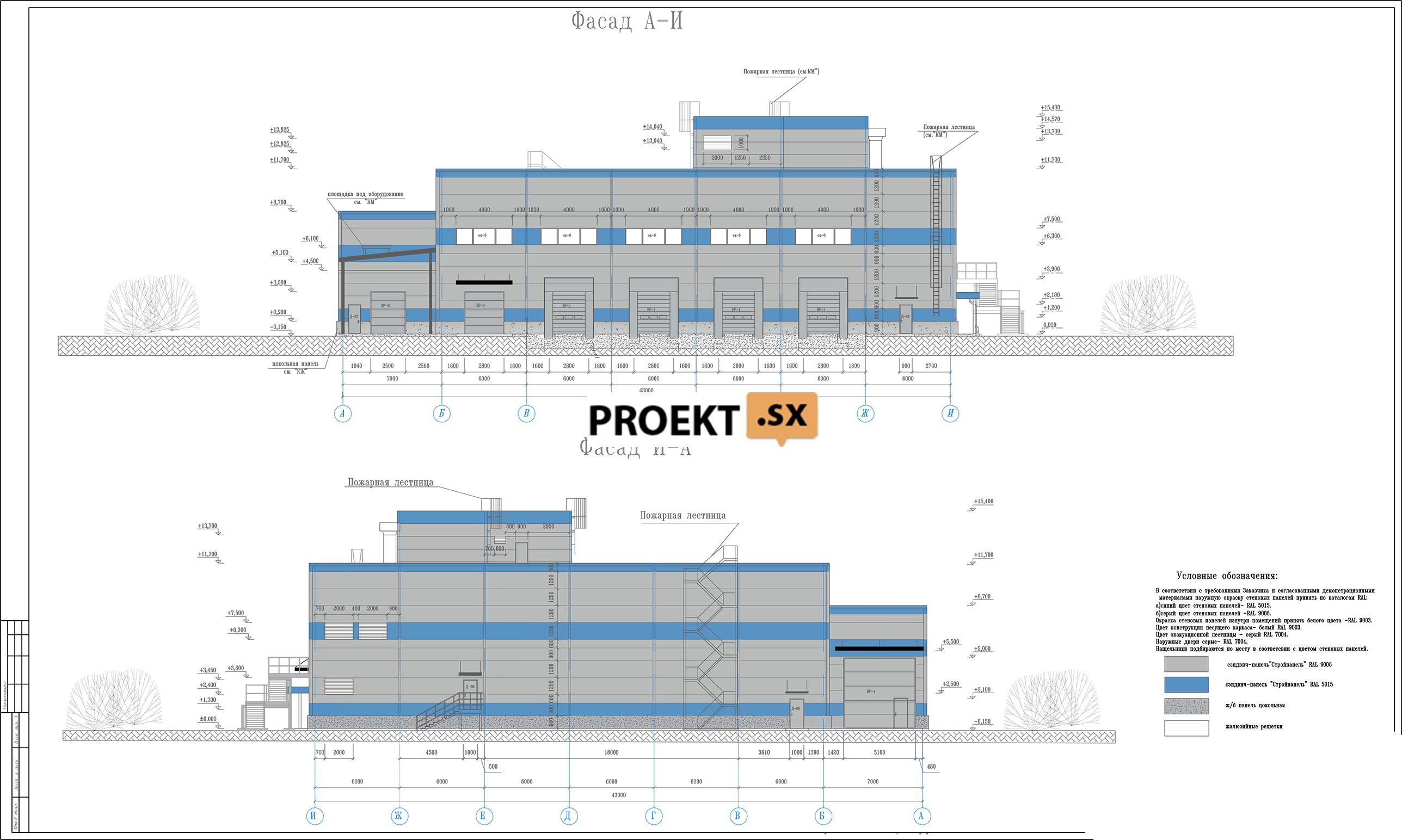
Площадь земельного участка, га: 2,32
Площадь застройки, м2: 5657,9
Строительный объем, м3: 45698,4
Объемно-планировочные решения
Объект представляет собой одно этажное здание прямоугольной формы размерами в плане 43 х 108 м и высотой до края парапета 11.7м. В здании объекта в осях 7-15/Е-И предусмотрено устройство двухэтажной встройки, в которой предусматривается размещение административно – бытовых помещений. Стены данных помещений выполнены из газобетонных блоков толщиной 250 мм с требуемым пределом огнестойкости EI45 мин. Заполнение оконных и дверных проемов выполнены с требуемыми пределами огнестойкости. Вход сотрудников в производственный цех осуществляется через встроенные административно-бытовые помещения. Для работающего персонала в соответствии с нормами РФ предусмотрены санузлы. Данные помещения располагаются во встроенном административно–бытовом блоке в осях 14-15/Е-Ж. Выходы предусмотрены в производственное помещение № 1.23. Двери выполнены с требуемым пределом огнестойкости. В производственной зоне также располагаются: Помещение компрессорной (№1.32). Стены данного помещения выполнены из сэндвич-панелей толщиной 120мм и газобетонных блоков толщиной 200мм. Помещение водомерного узла (№1.33) Стены данного помещения выполнены из сэндвич-панелей толщиной 120мм и газобетонных блоков толщиной 200мм. Помещение встроенной котельной (№1.34). Стены данного помещения выполнены из сэндвич-панелей толщиной 120мм и газобетонных блоков толщиной 200мм. В данном помещении предусмотрены легкосбрасываемые конструкции площадью 8,64кв.м. Помещение трансформаторной (№1.35,1.36) и помещение электрощитовой (№1.37). Стены данных помещений выполнены из газобетонных блоков толщиной 200мм Помещение лаборатории (№1.38). Стены данного помещения выполнены из газобетонных блоков толщиной 250мм. Все перегородки производственного цеха выполнены из материалов с требуемым пределом огнестойкости EI45. За отметку 0,000 принята отметка чистого пола производственного цеха =16.45 в Балтийской системе координат. Ограждающие конструкции Наружные стены цеха выполнены из сэндвич – панелей с минеральной теплоизоляцией толщиной 120 мм в соответствии с теплотехническим расчетом, цвет панелей с наружной стороны- RAL 9006 (серый), внутренней стороны - RAL 9002(белый). Покрытие – утепленное из минераловатных плит по профнастилу.
Описание технологического процесса производства
Производство включает в себя:
- зоны разгрузки и погрузки автотранспорта;
- зона складирования исходных веществ и материалов;
- производство;
- зона складирования готовой продукции;
- лаборатория входного контроля.
Предлагаемое предприятие будет состоять из одной производственной линии, установленной по овальному контуру, конвейер который будет двигаться непрерывно и с постоянной скоростью. Эта производственная линия будет оборудована двумя разными типами носителей, на которых монтируются формы для конечного продукта. Пенополиуретан получается путем смешивания химикатов при высоком давлении и непосредственно перед заливкой смеси в так называемую открытую форму. Используемыми при этом первичными химикатами являются смеси смол (метилендифенил диизоцианат) и полиола. Формы перемещаются в закрытом состоянии и подогреваются системами горячей воды, установленными на конвейере. Подушки из пеноматериалов вынимаются из формы, разминаются, подрезаются, ремонтируются, осматриваются и подготавливаются к отгрузке в адрес заказчика. Сырье – доставляется автотранспортом. Для хранения исходных компонентов предусматривается зона которая вмещает 4 резервуара объе6мом 50 куб.м. и 1 резервуар 18 куб.м. (ТДИ). В 3-х полиол и 2-х содержатся диизоцианаты. Для хранения парафина – растворителя в 200 – литровых бочках предусматривается отдельное помещение. Для разгрузки химикатов устанавливаются разгрузочный насос, а также замкнутая система возврата паров. Во время разгрузки пары вытесняются обратно в автоцистерну. Автоцистерны с полиолом разгружаются под давлением воздуха. Баки оборудуются системами предотвращающими переполнение, которые при срабатывании автоматически прекращает процесс разгрузки. Перед началом разгрузки проводится автоматическое испытание клапана переполнения. Во время перемещения материала в баки пеноуловители из производственной линии дыхательный клапан предотвращает возникновение вакуума в этом баке. Защита от повышенного давления обеспечивается наличием разрывной мембраны и расширительного клапана. На полностью автоматизированном участке предварительного смешивания полиолы перекачиваются из хранилища в бак смешивания, где они соединяются с другими химикатами для получения, при необходимости, различных смесей смол в замесовых смесях. После того как смесь смол будет получена, она заканчивается в специально предусмотренный бак выдержки. Для смол предусмотрено от шести до десяти баков вместимостью 2 м3 (максимум), один бак вместимостью 3,5 м3 для переделки замесов и один бак вместимостью 1,5 м3 для окрашивающей смеси. В связи с наличием паров аминов во время смешивания в контуре предварительного смешивания, в верхней части этого контура установлена местная вытяжная камера, в которой собираются все пары. Контур предварительного смешивания включает в себя блендерную установку к которой подсоединены различные потоки, бак предварительного смешивания вместимостью 1000 л, небольшой бак для катализатора и еще меньший бак-бюретка. В блендерную установку попадают следующие различные потоки: - потоки из среднетонажных контейнеров для насыпных грузов и барабанов, содержащих такие химикаты, как катализаторы, ингибиторы горения, поверхностно-активные вещества. Эти химические вещества перекачиваются отдельными насосами, предназначенными для работы с каждым из продуктов; - потоки полиола, идущие из насыпных баков полиола; - потоки воды, идущие из сети водоснабжения завода. Все эти химикаты подаются на блендер и оттуда в специальный бак – в бак предварительного смешивания ( 1000 л ), в очень маленький бак- бюретку (от 10 л до 20 л) и в небольшой бак катализатора (обычно от 50 л до 100 л). В каждом баке (предварительного смешивания, бюретке и для катализатора) имеется три загрузочные ячейки. Каждый из указанных выше химикатов должен отдельно закачиваться в конкретный бак так, чтобы дозировано подавалось правильное количество химиката с учетом размера загрузочных ячеек. Содержимое из бака для катализатора и бака-бюретки закачивается в бак для предварительного смешивания в соответствии с составом, введенным в компьютерный блок управления. Окончательный замес перекачивается в соответствующий бак выдержки. Жидкие химикаты с контролем их температурного состояния поступают из уравнительных баков по герметизированным трубам с помощью насосов высокого давления в смесительную головку высокого давления, которая монтируется на промышленном шестиосном роботе, в надлежащих пропорциях с помощью робота и смесительной головки раздаются при высоком давлении в пространство (открытой) формы. Количество заливаемого материала программируется заранее, а пропускная способность оборудования контролируется. Процесс пенообразования начинается тогда, когда положение смесительной головки меняется так, что потоки полиола и диизоцианата оказываются перемешанными при высоком давлении. В этот момент смесь падает вниз в форму, а рециркуляция прекращается, предотвращая смешивание в обратном потоке в направлении к уравнительным бакам. Когда заливка прекращается, смесительная головка отходит назад в первоначальное положение циркуляции. Как только заливка будет закончена, форма закрывается и начинается процесс отверждения при нагревании, когда форма нагревается до температуры 65°С с использованием горячей воды и электронагревателей. Производственная линия Производственная линия состоит из подвесного цепного конвейера с 44 держателями форм, в которых находятся формы. Формы открываются и закрываются на станции автоматического открывания. Производственная линия работает непрерывно с постоянной скоростью. Формы Используются формы двух различных типов – стандартная форма, которая имеет только механическое уплотнение, и типовая форма в которой для уплотнения формы при ее закрытии применяются воздушные подушки. Нагрев Формы подогреваются с помощью электрических водогрейных котлов. Нагревательные установки поддерживают температуру формы на уровне, необходимом для обеспечения эффективной и полноценной реакции химических продуктов. Вынимание из формы После того как форма автоматически откроется, набивка вручную вынимается и помещается на конвейер для отделки. Пустая форма перемещается в зону очистки. Очистка формы Очистка формы включает в себя удаление брызг пены или любых иных остатков пены, которые прилипли к стенкам формы во время вытаскивания. После того как форма будет вычищена, она готова к нанесению разделительного компонента. Нанесение разделительного компонента Нанесение разделительного компонента на формы является необходимой и важной функцией при производстве формованных пенополиуретановых изделий. Этот процесс можно разбить на три основных функции. Первая функция – это хранение и доставка материала. Вторая функция заключается в фактическом нанесении разделительного компонента на форму, а третья функция – удаление. Линия нанесения парафина Процесс нанесения разделительного компонента полностью автоматизирован. На базовой установке используются распылительные пистолеты, которые наносят разделительный компонент на формы. Количество разделительного компонента, подаваемого на каждый пистолет, дозируется независимо высокоточным регулятором, обеспечивая максимальный контроль за пропускной способностью. По мере того как движущаяся форма подходит через батарею распылительных пистолетов, каждый пистолет начинает действовать как раз на тех участках, на которые требуется нанести разделительный компонент. Каждая форма программируется независимо, и можно отключать те формы, в которых не производится изготовление изделия. Вместе с нанесенным разделительным компонентом форма перемещается в зону вставки. Вставка Вставки формы (рамы сидений и опорные ребра, ткань, препятствующая разрыву, и т. д.) помещаются в форму вручную. После того как эти вставки будут надлежащим образом размещены, форма готова для заливки в нее жидких химических продуктов в зоне работы заливочного робота. Перед тем как форма будет помещена в зону заливки, форму необходимо осмотреть на предмет правильного положения и размещения применяемых вставок с помощью системы CIS ( система контроля компонентов). Только в том случае, если эта система выдаст сигнал готовности, можно начинать заливку формы. После того как пенная часть будет вручную вынута из формы, она помещается на ленту конвейера для осуществления этапов отделки. Разминание. Пена сдавливается для того, чтобы открыть закрытые ячейки в пене и обеспечить устойчивость размеров ячеек во время охлаждения. Это осуществляется путем прохождения пенной части через ролики с узким зазором между ними или путем обработки пенной части в вакуумной камере при пониженном давлении. На заводе должна быть установка для роликового разминания или одна установка для вакуумного разминания. Подрезка. Подрезка производится (после разминания) для тех пенных частей, на которых имеются чрезмерные брызги или лишняя пена. Контроль. После визуального контроля пенные части либо получают разрешение на отгрузку, либо отправляют на ремонт, либо бракуются. После выполнения ремонта производится повторный контроль пенной части. Этот цикл повторяется до тех пор, пока пенная часть не получит разрешение на отгрузку. Пенные части, для которых дано разрешение на отгрузку, упаковываются и направляются в зону отгрузки (на склад) для отправки в соответствии с графиком отгрузки. Ремонт. Любые пенные детали с недопустимыми недостатками должны быть подвергнуты ремонту. Ремонт производится вручную с использованием других пенных подушек и клея. Можно использовать клей на водной основе или термоплавкий клей. Затем подушку нужно подрезать и осмотреть.